The number one concern I continue to hear about in every conversation with manufactures is they are hiring and there is not enough skilled or available labor to do the job. One of the worst things for a company to face is to have the work available but no way to execute in the time needed.
Beyond creating added stress to your workforce, labor shortages also contribute to increased workplace injury, increased product defects and loss in revenue. It is becoming more apparent that the way to sustainable growth is through the world of automation and innovation.
Automating in the right way can reduce the number of people needed to do the job as well as simplifying the task, making the position easier to hire and train for. It can also quickly add production capacity, with fast ROI’s when removing unnecessary touch and handling, it is a no brainer for most. Even the smallest of shops can outperform competitors when they add automation.
With that in mind LS Industries has just released a newly designed handling system. This is just one of many custom designed solutions to aid customers in the fight against labor shortages. What do our customers have to say?
“Safety- The transfers can be loaded and unloaded from the outside or 1st position. This way the operator doesn’t need to go in between the transfers to deposit or remove pieces closer to the conveyor.”
“Parts wear- Short 50” shuttle distance results in less wear on chains and sprockets.”
“Drag-Off transfers constantly need the drag dogs replaced. They are noisy and wear the conveyor rollers as they drag the material off the conveyor. They also can damage the infeed conveyor when material being loaded is jammed against the conveyor datum. Also operators drag the beams into one another which results either try to overload the drag dogs (too much weight) and pinning the beams flanges against one another where you can’t attach lifting clamps or get a chain around the pieces to stack.”
“Regular Lift and Carry transfers see a lot of chain and sprocket wear due to chain tension associated with tightening the chain to lift the buggy. They are also subject to broken springs on the buggy. Operators also misuse these by pushing material on the transfer with the raised buggy. This wears and damages the system and again can result in no gap between pieces for attaching chains or clamps.”
This new transfer design can be designed around any piece of equipment where there is a need for more automation. Want to learn more or need help with your handling, reach out to LS Industries for a chat.
*Shot Blasters *Parts Washers *Ovens *Paint Booths *Handling *Dust Collection *Downdrafts *Crankshaft Grinders *Flywheel Grinders *Balancers *Honing
Melissa Gibson – East Coast Sales Manager
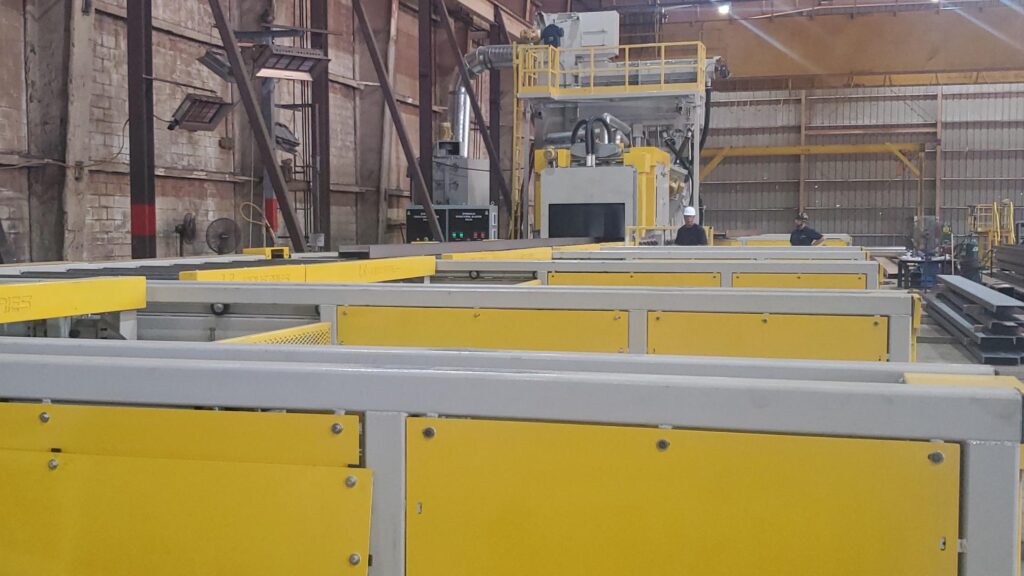